摘 要:介紹了鹽酸合成爐生產(chǎn)工藝流程,分析了影響合成爐安全運(yùn)行的因素并對運(yùn)行過程出現(xiàn)的問題提出了解決措施。
甘肅稀土新材料股份有限公司燒堿廠(以下簡稱燒堿廠),高純鹽酸 6 萬 t/a ,鹽酸合成爐為正壓式下自動點(diǎn)火三合一鹽酸合成爐(型號 SYHL-200 )。 由氯氫處理來的氯氣和氫氣分別經(jīng)過氯氣緩沖罐、氫氣緩沖罐、 氫氣阻火器和各自的壓力及流量調(diào)節(jié)閥,以一定的比例(氫氣、氯氣體積比 1.10∶1~1.40∶1 )進(jìn)入石墨合成爐底部的石英燈頭,氯氣走石英燈頭的內(nèi)層,氫氣走石英燈頭的外層,二者在石英燈頭前混合燃燒,合成的氯化氫向上經(jīng)冷卻吸收與尾氣塔來的稀酸一起吸收制成鹽酸,未被吸收完全的尾氣(大部分是不凝性氣體) 經(jīng)過尾氣吸收塔再次吸收處理達(dá)標(biāo)后排放。 冷卻水罐的純水由泵輸送至石墨合成爐冷卻段和吸收段與合成氯化氫的溶解熱進(jìn)行熱交換,然后經(jīng)過板式換熱器,與循環(huán)水冷卻后回到冷卻水罐,如此循環(huán)。 針對鹽酸合成工藝運(yùn)行過程中易出現(xiàn)的突發(fā)問題 (比如原料氣純度不夠、造成氯氣外泄等;吸收水?dāng)嗔,造成爐溫、爐壓升高緊急滅爐;氯氣、氫氣流量波動,緊急聯(lián)鎖滅爐;操作不當(dāng)造成氫氯比例失調(diào))。 故在生產(chǎn)實(shí)際應(yīng)做好以下檢查工作。
1 開車前原料分析與工藝檢查
三合一鹽酸合成爐可使用原氯、尾氯或混合氯生產(chǎn)鹽酸, 原料氣的指標(biāo)包括氫氣體積分?jǐn)?shù)大于98% ,氫中樣體積分?jǐn)?shù)小于 0.4% ,氯的體積分?jǐn)?shù)大于 70% ,氯中氫的體積分?jǐn)?shù)小于 2% 。 造成氫氣純度下降因素:( 1 )氫氣系統(tǒng)溫度高,含水高;( 2 )氫氣系統(tǒng)雜氣高(如氮?dú)猓;?3 )合成爐在使用氮?dú)庵脫Q過程存在死角。
在點(diǎn)爐之前分析氫氣及氯氣的相關(guān)指標(biāo),尤其是氫氣指標(biāo)分析,且根據(jù)實(shí)際生產(chǎn)情況,確保置換時(shí)間和壓力, 在爐體雜氣置換過程中不留死角,防止在點(diǎn)爐過程出現(xiàn)氫氣爆鳴等。 其次,對前道工序進(jìn)行檢查, 尤其是電解系統(tǒng)充氮置換管線閥門檢查。 采取氮?dú)獯祾邭錃夤艿,且氮(dú)馕锢硇再|(zhì)與氫氣性質(zhì)相似,都不溶于水,使用焦性沒食子酸吸收氫氣中的氧,測定氫氣純度。 該方法不能識別氫氣系統(tǒng)是否含有氮?dú),故在全線停車后,再次開車,必須檢查電解氫氣充氮系統(tǒng)閥門,防止氮?dú)膺M(jìn)入氫氣系統(tǒng) [1] ,造成氫氣不純,出現(xiàn)過氯;其次是及時(shí)檢測鹽酸濃度和鹽酸中游離氯的含量, 不能僅將氯氣、氫氣流量及體積比值作為安全運(yùn)行判定的依據(jù);#后,在生產(chǎn)過程中對氫氣系統(tǒng)溫度進(jìn)行嚴(yán)格控制。
2 吸收水系統(tǒng)檢查
吸收水?dāng)嗔,爐內(nèi)氯化氫氣體在短時(shí)間內(nèi)大量累積,爐壓、爐溫升高,尾氣管炸裂。 吸收水?dāng)嗔髦饕蛴屑兯到y(tǒng)供應(yīng)出現(xiàn)障礙和吸收水泵故障。
( 1 )吸收純水生產(chǎn)系統(tǒng)故障
由于生產(chǎn)系統(tǒng)純水制備工序蒸汽與鹽水精制工序使用同一蒸汽系統(tǒng)。 生產(chǎn)系統(tǒng)蒸汽壓力下降,含堿化鹽水串入蒸汽系統(tǒng),導(dǎo)致回收至純水系統(tǒng)蒸汽冷凝水含堿升高,進(jìn)入純水反滲透膜,導(dǎo)致 RO 反滲透膜通量急劇下降,純水產(chǎn)量故障,造成緊急停爐;其次,定期檢測純水生產(chǎn)系統(tǒng)回收蒸汽冷凝水的 pH 值及電導(dǎo)率, 防止回收冷凝水含堿高等造成純水質(zhì)量波動,被動生產(chǎn)。
( 2 )吸收水泵不上液
在正常倒泵過程中,吸收水泵突然斷流,再次起停仍不上液,泵腔吸入空氣,打破泵腔真空度,極易造成泵不上液。
在設(shè)計(jì)時(shí)未考慮到當(dāng)?shù)貧夂驐l件,均未裝設(shè)泵腔排氣閥, 崗位操作人員在倒泵過程中, 啟動泵時(shí)泵腔未進(jìn)行排氣, 導(dǎo)致運(yùn)行泵時(shí)泵腔吸入空氣,吸收水?dāng)嗔,爐內(nèi)氯化氫氣體含量急劇上升導(dǎo)致爐壓升至 26 kPa ,尾氣管線斷裂,稀酸外泄,執(zhí)行緊急停爐,降電流。 對此,在吸收水泵進(jìn)口各加裝 DN25 排空閥,在啟用備用泵之前,先用吸收水進(jìn)行灌注,排氣后再啟泵, 停用泵使用排空閥對泵腔進(jìn)行排空,防止吸收水管線凍結(jié)。
3 正常生產(chǎn)監(jiān)控
生產(chǎn)中, 一般要求保持氫氯比例在 1.10∶1~1.35∶1 , 氫氣、 氯氣的#佳流量是根據(jù)爐內(nèi)火焰顏色、氣體的實(shí)際純度及壓力,及時(shí)觀察鹽酸濃度、游離氯含量、氫氣流量調(diào)節(jié)閥及氯氣流量調(diào)節(jié)閥的開度。 在夏季生產(chǎn)中,氫氯比值稍高一般控制在 1.27~1.35 ,夏季氣溫高,生產(chǎn)系統(tǒng)溫度稍高于冬季溫度,氫氣含水量較大,比值過低(實(shí)際生產(chǎn)低于 1.25 ),極易出現(xiàn)游離氯升高現(xiàn)象,即合成爐過氯;其次,及關(guān)注合成爐冷卻系統(tǒng)溫度, 板換壓力等工藝參數(shù),如果循環(huán)水冷卻水長期在 40~60 ℃ 運(yùn)行,極易在合成冷卻板換中形成鈣質(zhì)結(jié)垢, 堵塞換熱系統(tǒng),造成合成爐下酸溫度升高,極易造成緊急停爐,及時(shí)倒板換并清理;做好循環(huán)水水質(zhì)監(jiān)測和敞開式循環(huán)水池防護(hù)工作,尤其春秋季節(jié),風(fēng)沙或落葉較多進(jìn)入循環(huán)水系統(tǒng),極易堵塞板換,造成爐體溫度升高;在工藝檢測中,及時(shí)觀測爐體冷卻水溫度、溫差及板換運(yùn)行壓力,溫差越低或板換壓力有逐漸升高趨勢,說明板換堵塞換熱效果下降,及時(shí)倒板換進(jìn)行清理。 冬季生產(chǎn)時(shí)確保氯氣輸送溫度及氫氣輸送溫度,尤其是在北方寒冷天氣,氫氣系統(tǒng)使用蒸汽伴熱管伴熱,否則易出現(xiàn)進(jìn)合成爐阻火器因積水或因腐蝕的銹渣堵塞阻火器,造成進(jìn)爐氫氣調(diào)節(jié)閥開度開至 90% 以上,但流量仍不能滿足使用要求,必須及時(shí)倒?fàn)t,清理阻火器;其次,冬季生產(chǎn)時(shí)氫氣溫度過低,氫氣管道積水增多,氫氣壓力不穩(wěn),或由于冷凝水含量過高造成合成爐燈頭炸裂也是導(dǎo)致合成爐緊急滅爐的關(guān)鍵因素之一,冬季生產(chǎn)加強(qiáng)氫氣系統(tǒng)排水,防止冷凝水聚集。
4 合成爐停爐操作
在合成爐停爐操作過程中, 必須在確保氫氯配比的情況下, 先降低氯氣流量, 再同步降低氫氣流量,吸收水流量同步降低。 切忌先降氫氣流量或吸收水流量,若先降氫氣流量,極易造成氫氯比例失調(diào),緊急滅爐;吸收水降低過快,爐內(nèi)氯化氫氣體含量過高,極易造成爐壓升高、尾氣炸裂、鹽酸外泄污染環(huán)境等事故。 停爐之后,對爐體進(jìn)行充氮保護(hù)。
5 自動控制系統(tǒng)
鹽酸合成爐系統(tǒng)自動化程度水平已經(jīng)很高,已實(shí)現(xiàn)在線火焰監(jiān)控、氯氫流量調(diào)節(jié)、吸收水流量調(diào)節(jié)、比值聯(lián)鎖安全保護(hù)、氯氫壓力聯(lián)鎖保護(hù)、充氮系統(tǒng)及整流跳閘聯(lián)鎖保護(hù)等安全裝置。 工藝聯(lián)鎖簡圖見圖 1 。在實(shí)際運(yùn)行中,及時(shí)檢查氯氣壓力變送器等,防止由于氯氣系統(tǒng)酸泥累積造成差壓變送器失靈,流量、壓力不準(zhǔn)確;其次是前系統(tǒng)氫氣或氯氣壓力波動,造成進(jìn)入合成系統(tǒng)氫氣、氯氣壓力急劇降低至聯(lián)鎖跳閘保護(hù)值等緊急滅爐;檢查工藝過程中聯(lián)鎖正確投入,對爐體和安全運(yùn)行進(jìn)行保護(hù)。
6 結(jié)語
鹽酸生產(chǎn)中使用氯氣及氫氣危險(xiǎn)性比較大,且鹽酸泄漏極易造成環(huán)境污染,故在合成爐操作過程中及緊急情況,對操作人員的熟練程度和安全意識
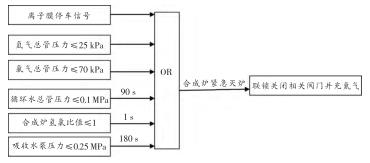
要求極高;其次,必須嚴(yán)格監(jiān)控各項(xiàng)工藝指標(biāo)和嚴(yán)格按照操作規(guī)程執(zhí)行;在日常生產(chǎn)中,加強(qiáng)實(shí)踐,不斷完善自控系統(tǒng)。
注明,三暢儀表文章均為原創(chuàng),轉(zhuǎn)載請標(biāo)明本文地址